ErgoTEC usa impresión 3D y novedosos métodos para hacer prótesis mejores y más baratas
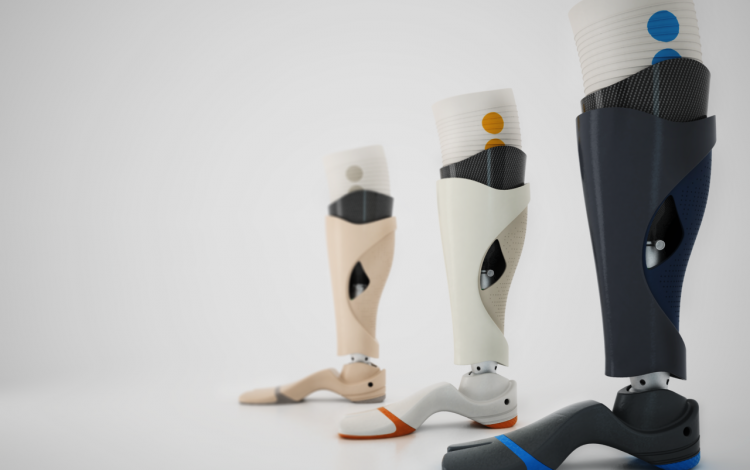
Imagen con fines ilustrativos. Propuesta de diseño de Miguel Araya para su tesis de grado en Ingeniería de Diseño Industrial. Foto: Cortesía M. Araya.
- Proyecto busca abaratar las prótesis para quienes perdieron un pie.También permitirá acelerar el proceso de ajustar el dispositivo, que en la actualidad toma hasta dos años.
Por medio de la impresión 3D y la utilización de innovadores materiales, los especialistas de ErgoTEC, del Tecnológico de Costa Rica, buscan que el proceso de creación de prótesis en el país sea más rápido y barato.
El proyecto “Aplicaciones tecnológicas para el diseño y desarrollo de prótesis transtibial de bajo costo” utiliza tecnología de punta para que las personas amputadas de la rodilla para abajo puedan recuperar su vida tan pronto y fácil como sea posible.
“Actualmente, en nuestro país tenemos algunas características o condiciones para el desarrollo de prótesis en las que hemos visto oportunidades, debido a que existen necesidades importantes en este campo. Las necesidades principales son que hay una gama de productos muy limitada y son en muchos casos de elevados costos”, explica el ingeniero en Diseño Industrial Miguel Araya, a cargo de la investigación que inició en enero de 2016 .
Según el experto, en la actualidad en Costa Rica una prótesis transtibial puede costar entre $1.000 y $15.000, dependiendo del nivel de funcionalidad; mientras que el Seguro Social dispone de subvenciones de entre ₡325.000 y ₡375.000 (unos $675, al tipo de cambio del 30 de noviembre) para atender a las personas que hayan perdido parte de sus piernas y no cuenten con los recursos necesarios para comprar una prótesis por sus propios medios.
Adicionalmente, en el Taller Nacional de Ortesis y Prótesis (TNOP), que es la única opción que da el Seguro para recibir una prótesis, tiene listas de espera que provocan que un paciente espere hasta un año para recibir una prótesis.
“Hemos visto casos de pacientes que duran hasta dos años en recibir la prótesis definitiva. Es un proceso largo y, en opinión de algunos doctores y expertos del tema, es importante tener una implementación lo más pronto posible dentro de lo que cabe para que la persona pueda tener una adaptación normal a la prótesis”, ahonda Araya.
Esta problemática se agrava, pues datos recopilados por ErgoTEC muestran que en el país hay más de 140.000 personas con discapacidad para caminar o subir gradas y el TNOP ha experimentado un aumento de 71% en la demanda de pacientes, principalmente en las amputaciones abajo de rodilla, con un crecimiento de un 187% en este tipo de casos.
Ventajas de la impresión 3D
Lo mucho que dura el proceso para recibir una prótesis se debe, en parte, a factores como que todos los componentes utilizados son importados y se requiere de un técnico especializado para tomar las medidas del paciente y personalizar la implementación, particularmente en la parte que hace contacto con la pierna del paciente.
Por eso el proyecto de ErgoTEC se centra en la utilización de nuevas técnicas de manufactura, como la medición en tercera dimensión y la impresión 3D, pues estos métodos permiten crear dispositivos mucho más detallados y elimina la necesidad de importar los componentes.
“Lo importante es buscar, mediante la tecnología y mediante nuevos procesos de manufactura y de diseño, tener como resultado una prótesis que tenga dos características: que sea de un menor costo que las existentes y que responda a la necesidad funcional de un paciente”, detalla Araya.
Es vital abaratar costos. Araya dice que una de las ventajas de la impresión 3D es que resulta más económica, pues en lugar de tener que extraer y desechar material para acoplar una pieza a la necesidad del paciente, utiliza el material justo para crear la prótesis.
Mas este nuevo proceso tiene muchas más ventajas:
- Permite hacer mejores diseños.Más adecuados a las características anatómicas del paciente.Ajustar los dispositivos a la necesidad funcional del paciente y su estilo de vida.Acelerar el proceso, ya que reduce la posibilidad de error al moldear la pieza.
“Estamos trabajando principalmente con reforzamiento de fibras, con materiales compuestos de fibras de carbono; posiblemente vamos a hacer algunas pruebas con kevlar (fibra artificial de gran resistencia que suele ser utilizada como material antibalas) y con fibra de vidrio. Estas fibras tienen un reforzamiento en una matriz polimérica.
“Lo que hacemos es, por medio de tecnologías existentes de manufactura aditiva, desarrollar probetas impresas en 3D y hacer ensayos mecánicos de esas probetas. Toda esa información de datos de caracterización mecánica de los materiales la vamos a tomar como insumo para el desarrollo del producto”, explica el experto.
Detalle de la propuesta de diseño que elaboró Miguel Araya para su tesis de grado en Ingeniería en Diseño Industrial con énfasis en Desarrollo de Productos. Este trabajo servirá de base para el proceso de creación de prótesis que desarrolla ErgoTEC. Foto: Cortesía M. Araya.
Baratas, rápidas y que gusten
Ya en su tesis de grado –junto al Ing. Eckart Holst–, Araya diseñó prótesis mucho más atractivas que las que suelen utilizarse actualmente. Este es un factor fundamental para los pacientes, pues el componente emocional juega un papel importante para que las personas sientan las ganas de usar las prótesis y rehabilitarse.
La impresión 3D favorece esto, pues permite hacer prótesis más personalizadas, adecuadas no solo a las necesidades de cada quien si no que también que sean mejor acopladas a sus cuerpos.
“Lo que estamos buscando principalmente es bajar los costos, pero también trabajar con la parte emocional, que es muy importante. Si nos ponemos a analizar, usualmente las prótesis existentes son muy tubulares, se adecuan a ciertas necesidades funcionales pero no por completo a las necesidades emocionales que tiene un paciente amputado (...).
“Lo que buscamos es que a través del diseño, y con otras tecnologías como el escaneo en 3D, podamos generar volúmenes de la otra pierna del paciente, si es que tiene la otra pierna, y de esa manera tomar medidas, las tomas antropométricas del paciente y generar un volumen que pueda ser producido”, comenta Araya.
El siguiente paso, que es desarrollar el prototipo y hacer pruebas de validación, estará listo en el primer semestre de 2017.
Para finales del próximo año, se espera que ErgoTEC pueda presentar al país un modelo realizable que permita fabricar, completamente en Costa Rica y con mayor celeridad, prótesis más baratas y adecuadas para sus usuarios.
Montaje de cómo se verían en uso las prótesis diseñadas por Miguel Araya. Fotos: Cortesía M. Araya.
Generar conocimiento
Uno de los principios fundamentales de ErgoTEC, explica Olga Sánchez, coordinadora, es propiciar a los investigadores y a estudiantes del TEC de espacios para generar conocimientos y habilidades.
“Los proyectos que se desarrollan en ErgoTEC tiene como objetivo principal impactar lo que es calidad de vida de las personas, poder aportar en ese sentido y propiciar que tengan un cambio significativo. Se trata de que puedan desarrollar las actividades cotidianas de mejor forma o evitar lesiones que puedan ser incapacitantes“, comenta Sánchez.
Es así como este proyecto se desarrolla de forma interdisciplinaria. Araya coordina la iniciativa como especialista en Diseño Industrial con énfasis en Desarrollo de Productos y en esta fase de la investigación se trabaja con estudiantes de Ingeniería en Materiales. En un futuro, se sumarán más estudiantes de grado y posgrado de diversas disciplinas.
También está en el proyecto Nicolette Chamberlain-Simon, pasante Rice University, de Houston, Texas, quien contribuye con su especialidad en bioingeniería.
“Estaba buscando un proyecto con prótesis de bajo costo y me gustaba mucho la idea de trabajar con impresión 3D, en eso este proyecto es muy prometedor (...).
“Yo me enfoco más en la parte más médica del desarrollo y trabajo mucho con la anatomía en el proceso de desarrollar una prótesis, así que espero aportar mucho en la etapa de diseño“, denota Chamberlain-Simon.