Investigación busca crear las mejores baterías de aluminio: menos contaminantes y más duraderas
- Se está estudiando cuál es la mejor aleación de aluminio y magnesio, que sirva como base para las baterías
- El aluminio es mucho más abundante, reciclable y menos contaminante a la hora de procesarlo, que el litio
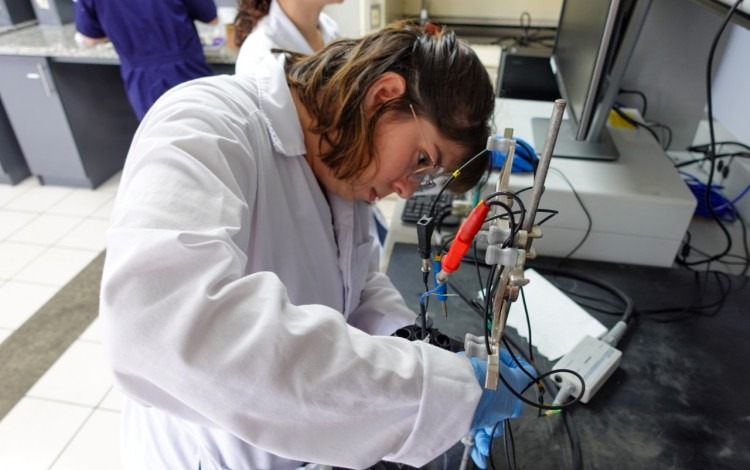
Andrea Alfaro Jiménez, estudiante de Ingeniería en Materiales, prepara el equipo para hacer pruebas electroquímicas de las baterías. Fotografía: Johan Umaña V.
El aluminio es el elemento metálico más abundante en nuestro planeta, hasta el 8% de la corteza terrestre está conformada por este elemento. Esto, y la facilidad para extraer y manipular este material, le hace particularmente útil. Es por eso, que personas investigadoras y estudiantes de la Escuela de Ciencia e Ingeniería de los Materiales, del Tecnológico de Costa Rica (TEC), quieren aprovechar el aluminio para hacer mejores baterías.
La investigación es guiada por el Dr. Jorge Cubero Sesín, y realizada por el M.Sc. Joaquín González Hernández, quien forma parte del Doctorado Académico en Ingeniería (posgrado conjunto del TEC y la Universidad de Costa Rica) y se enmarca dentro del proyecto VIE: “Aleaciones ligeras de magnesio y aluminio nanoestructuradas por deformación plástica severa para la fabricación y mejora de sistemas de almacenamiento de energía”. Además, el estudio es impulsado por el Programa de Investigación en Materiales Avanzados y Aplicaciones (PIMAA) y se colabora activamente con el Dr. Diego González, del Centro de Investigación en Electroquímica y Energía Química (CELEQ), de la UCR.
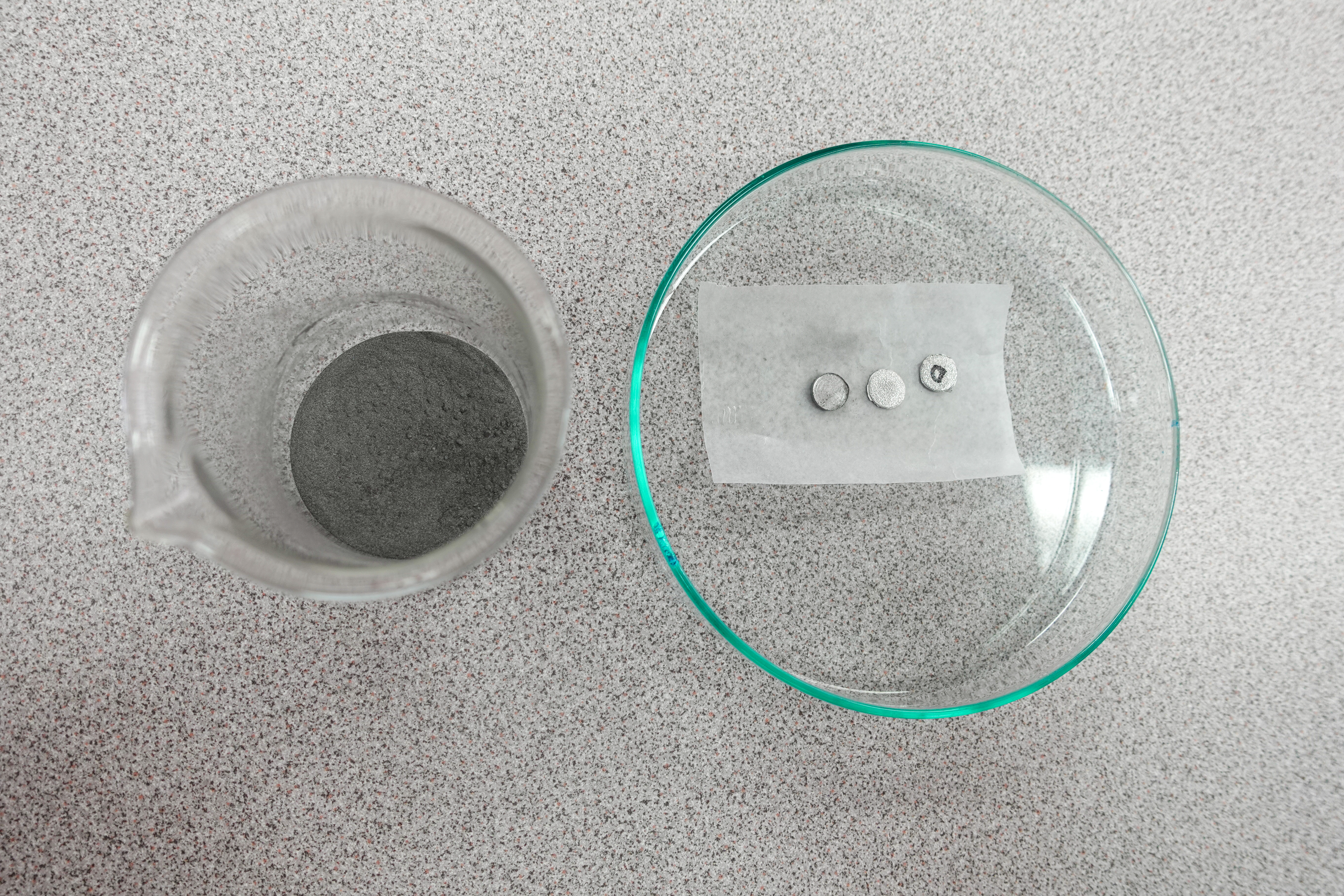
Es parte de los estudios en deformación plástica severa de materiales, y en esta etapa se centra en encontrar la combinación idónea de la aleación de aluminio (Al) y magnesio (Mg) para el óptimo funcionamiento de baterías de aluminio - aire. Primero en pequeña escala, con discos de 10 milímetros de diámetro y 1 mm de grosor, pero con la clara intención de continuar escalando el proceso.
“Ahora estamos en escala de laboratorio, haciendo mezclas para proporcionar una aleación que sea lo más eficiente posible. Ya de ahí lo vamos escalando y las aplicaciones ya irían en función del tamaño que queremos la batería, porque el método de procesamiento ahorita nos permite hacer una batería pequeña, que podemos utilizarla en teléfonos celulares, para cargar bombillos o dispositivos pequeños. Pero también, ya teniendo definido cuáles son las condiciones de formación y la estructura que queremos, que va a dar mayor eficiencia, podemos fabricar baterías más grandes, que se podrían utilizar en un automóvil eléctrico, por ejemplo”, explica González.
Según González, la principal ventaja de las baterías de aluminio es que el procesamiento de este material es mucho menos contaminante que el litio, material predominante en la amplia mayoría de baterías que se usan actualmente.
Otra virtud del aluminio es que es altamente reciclable, por lo que se podría pensar que una lata de refresco se podría reciclar en una pequeña batería de aluminio.
Para el Dr. Jorge Cubero Sesin, coordinador del Centro de Investigación y Extensión en Materiales (Ciemtec) y además mentor y coordinador del grupo de investigación en deformación plástica severa de materiales, este tipo de estudios muestra cómo la ciencia base puede tener efectos muy prácticos para mejorar la calidad de vida de las personas:
“Hemos venido consolidando un grupo de investigación en materiales nanoestructurados por deformación plástica severa desde hace 10 años, se ha desarrollado un laboratorio especializado y nos apoyamos en equipos de caracterización avanzada, tanto en el Ciemtec como en otros laboratorios de la Institución, para poder realizar investigaciones en materiales para aplicaciones biomédicas y en energía”, destacó Cubero.
Proceso de investigación
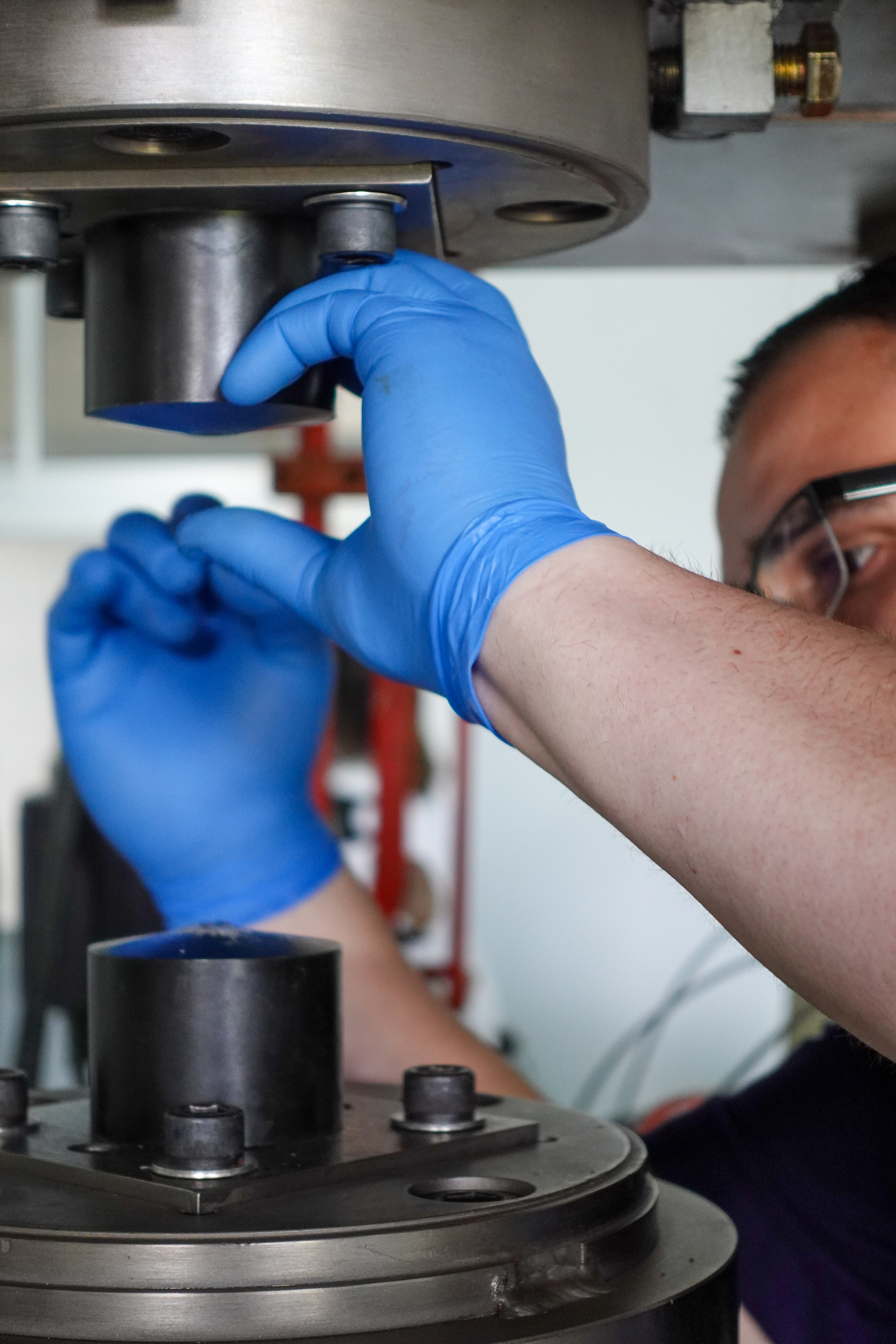
Esta investigación es posible gracias a la máquina de Máquina de Torsión a Alta Presión (High-Pressure Torsion o HPT, en inglés), del Centro de Investigación y Extensión en Materiales (Ciemtec), un equipo único en la región y que combina el poder de la alta presión y la torsión (hasta doscientas toneladas en un área pequeña pueden generar varios Gigapascales de presión) y torques de hasta 1.000 Nm, para modificar las estructuras atómicas de los materiales.
“Es una investigación de varias composiciones. Eso lo hacemos con polvos y variando la composición de cuáles van a ser los elementos aleantes y cuál porcentaje van a tener ellos dentro de la composición. Estas muestras primero se obtienen en polvos y se van a procesar para meterlas, en discos pequeños, en la Máquina de Torsión a Alta Presión, ahí se van a procesar por deformación severa”, explicó Andrea Alfaro Jiménez, estudiante de Ingeniería en Materiales.
Después de realizar distintas mezclas de aluminio y magnesio, sometidas a diferentes condiciones de presión y torsión, se pasa a la fase de pruebas.
“De la máquina obtenemos las muestras, en forma de pequeños discos, y pasamos a caracterizarlos, primero de forma microestructural. Hacemos un corte transversal de las muestras y ahí se ve el efecto del procesamiento a alta presión, donde se nota el flujo del material. Lo que esperamos ver es una microestructura homogénea”, detalló Tatiana Zamora Rojas, estudiante de maestría y otra de las investigadoras que trabaja en este proceso.
Finalmente, las baterías pasan a pruebas de rendimiento, para ir definiendo cuáles son los procesos que dan los mejores resultados y con los que podría trabajar en una futura etapa de escalamiento a mayor tamaño.
“Pasamos a la caracterización electroquímica, en las que se hacen pruebas para medir cuál de todas las aleaciones que estamos estudiando nos dan los mejores resultados en tiempo de descarga de las baterías”, ahondó Zamora.
Esta investigación ya ha dado por resultado la publicación de varios artículos científicos y la presentación en distinguidos congresos nacionales e internacionales.
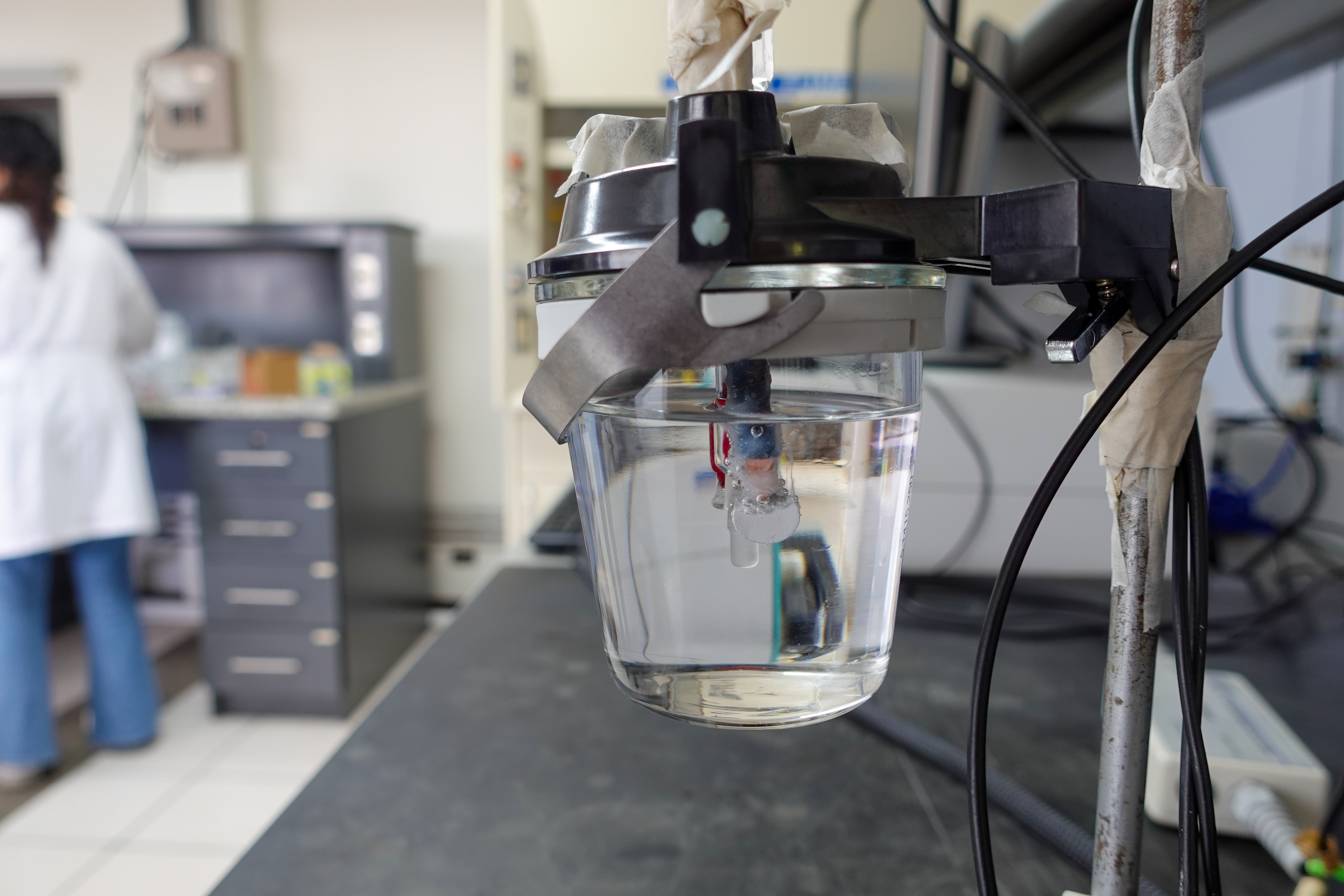